Alright, let’s talk about this thing – the area of thread engagement. Sounds pretty straightforward, doesn’t it? Like, you screw a bolt into a nut, and boom, engaged. That’s what I thought for a good while, anyway.
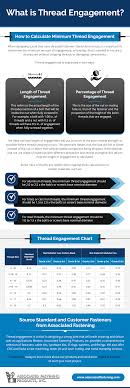
But then, you get that one project. Oh boy, that one project. We were putting together these new mounting brackets, custom job, looked great on paper. But when we started assembling them, things just weren’t holding. Bolts were stripping, or worse, pulling right out of the threaded holes in the softer material we were using for one part. It was a nightmare.
The Breaking Point (Literally)
We were burning through bolts and tapped holes like crazy. First, everyone’s blaming the bolt quality. “These must be cheap bolts!” Then it was, “Is this material too soft?” We tried different grades of bolts, harder materials where we could, but the problem just… persisted. It was maddening. Production was grinding to a halt, and the boss was starting to give us that look.
I remember spending a whole afternoon just staring at a failed connection. The threads on the bolt were mangled, and the internal threads in the part were just gone, like they’d been scooped out. It wasn’t about brute force; something more fundamental was wrong.
Someone, I think it was old Dave from the machine shop, just casually asked, “How deep are those threads actually grabbing?” And it was like a lightbulb moment. We were so focused on the diameter and the thread pitch, but not really on how much of those threads were actually doing the work.
Digging In
So, I started digging. Turns out, this “area of thread engagement” isn’t just about screwing it in till it’s tight. It’s about having enough surface area of the threads in contact to actually handle the load you’re putting on them. If you don’t have enough, well, you get what we got – stripped threads and a lot of scrap parts.
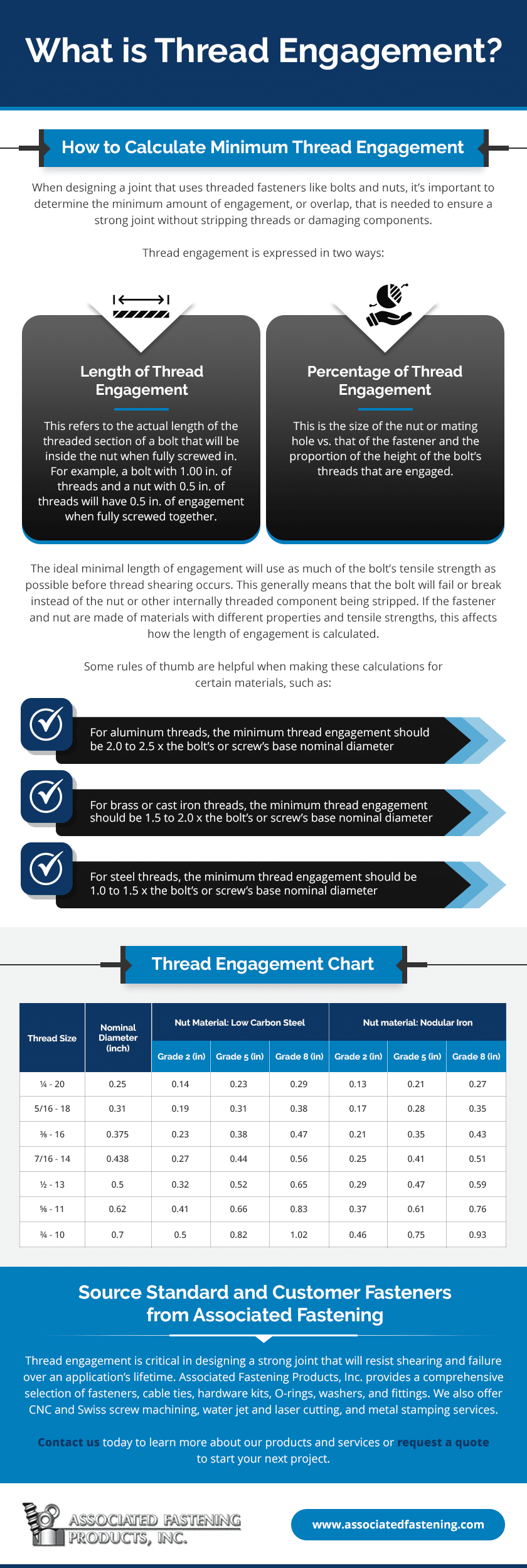
We found out the hard way that:
- Material matters a LOT. Screwing a steel bolt into aluminum? You need way more engagement length than steel into steel. The softer material just can’t take the same pressure per thread.
- It’s not just about depth. It’s about the effective depth, ensuring enough threads are properly formed and mating.
- Sometimes “standard” isn’t enough. Our design had relied on some standard assumptions for thread depth, but given the specific loads and materials, standard was failing us spectacularly.
We actually had to go back to the drawing board for a few components. We increased the thickness of the material where the threads went in, allowing for deeper tapped holes. For some critical spots, we even switched to using threaded inserts to give the bolts a stronger material to bite into. It felt like we were re-engineering the whole thing just for a few stupid bolts.
The fix wasn’t instant. We did a bunch of trial-and-error. Tapped a hole, put a bolt in, applied some torque, sometimes even rigged up a simple pull test. It was tedious, a real grind. Lots of “nope, stripped again” moments. But slowly, we started to get a feel for what worked for our specific application.
Finally, success. When we got the engagement lengths right, those connections were solid. No more stripping, no more pull-outs. It was a huge relief, let me tell you. Felt like we’d conquered a mountain, even though it was just about how a bolt screws into a hole.
So yeah, area of thread engagement. It sounds like a tiny detail, but man, get it wrong, and it can derail your whole project. It’s one of those things you learn the hard way, and then you never, ever forget it. Definitely added a few gray hairs, that particular lesson did.
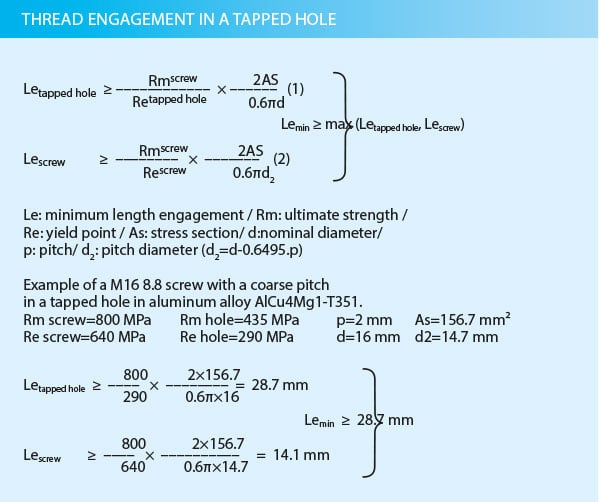